An other Interesting Order to Indonesia: High-Pressure Gate
ARMATURY Group dispatched two huge pieces of high pressure gate valves S43 DN 600 to Indonesia. The complete 3,3 m high armature, including the mounted control, weighed a respectable 6,500 kg.
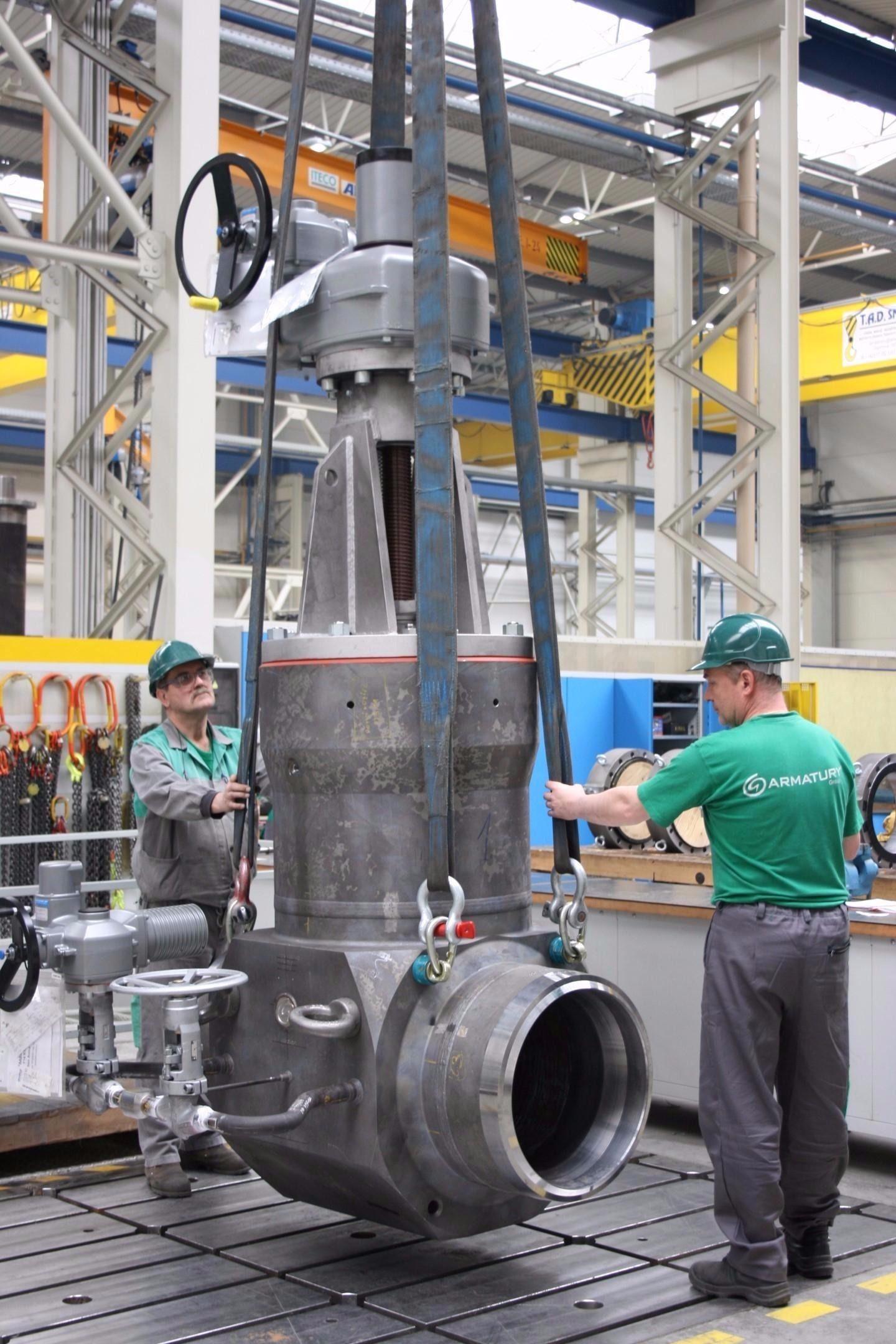
Last year, our company has won a very interesting order, namely a delivery of two pieces of high-pressure gate valves S43 DN 600 PN 250 to Indonesia.
The gate valves are designed for very high service parameters and are operated by a spur gear operator and electric actuator made by AUMA. The service fluid is steam with a pressure of 121 bar at a temperature of 530 °C. The gate valves are to be connected to a piping made of ASTM A335 P91 (hereinafter referred to as P91) the dimensions of which are 610 x 36.53 mm in the pulp and paper mill.
“From the very beginning of preparation of that order, I deliberated how to come to the lowest possible price and, at the same time, to meet safety requirements and specifications of the customer. Taking account of the high price of the P91 material, we decided to offer a gate valve combining two materials,” says Petr Postulka, designer, when describing how the work started. What were the materials? “We chose 14MoV6-3 for the main body and the extension piece. High-grade steel P91 is used only for the valve body ends (end connections) that are to be joined with the piping directly. The weight of the forging of the main body was 6,800 kg before machining but only 2,800 kg after machining, which means that the majority of the steel material ended as scrap in form of metal chips. For that reason we suggested the alternative with a different steel grade (14MoV6-3) that meets the service requirements and is more favourable in economical terms. Then the extension piece, made also of 14MoV6-3, for installation of the bonnet was attached to the body by welding and finally the end connections made of P91 were welded to the body,” adds Petr Postulka. The weight of the whole body weldment was 4,230 kg.
Heavy-Duty Gate Valve
The gate valve is designed as a heavy-duty valve, which means that also other parts of the gate valve are adapted to this fact. “Seating surfaces of the seats and the wedge gate are hardfaced with Stellite 6, which is the most suitable material for the fluid to be transported. The body-bonnet joint is made as a pressure seal joint sealed with a profiled graphite ring. Protection against pressure increase in the valve body cavity is provided by a double bypass system with a nominal size of DN 40,” explains Petr Heider, the Technical Director. The gate valve was subjected to shell strength tests according to European Standards with satisfactory results.
Because of the great size of the gate valve, different problems had to be solved during its production, such as handling of different gate valve parts, machining of individual valve parts and components, provision of new qualifications for welding procedures and welders, and preparation of fixtures for plasma hardfacing of seating surfaces and assembly of individual valve parts and components.
New Technology Used
“In order to improve welding of the 14Mo6-3 steel grade, we used a new technology of automatic submerged arc welding with tubular cored wire with basic filling, international welding process number 125. The weld with a diameter of 780 mm has a thickness of 67.5 mm,” adds Ludmila Hoňková, the Chief Welding Technologist. “By using this technology we were able to reduce the welding time from 14 hours as initially planned to 6 hours. All welding activities were done at a temperature of 200-250 °C. Preheating was done in a furnace for automated process and manual welding of the combination of P91 and 14MoV6-3 materials by means of heating pads with resistance heating. Quality of all welds was examined by radiographic method and magnetic particle examination of surfaces,” continues Ludmila Hoňková and adds that this part of production was challenging for both the pre-production personnel and the production workers. “Partial activities required utmost concentration more than ever,” she concluded.