New robotic welding workstation
Another significant investment in the machinery of the ARMATURY Group is the newly installed robotic welding workstation.
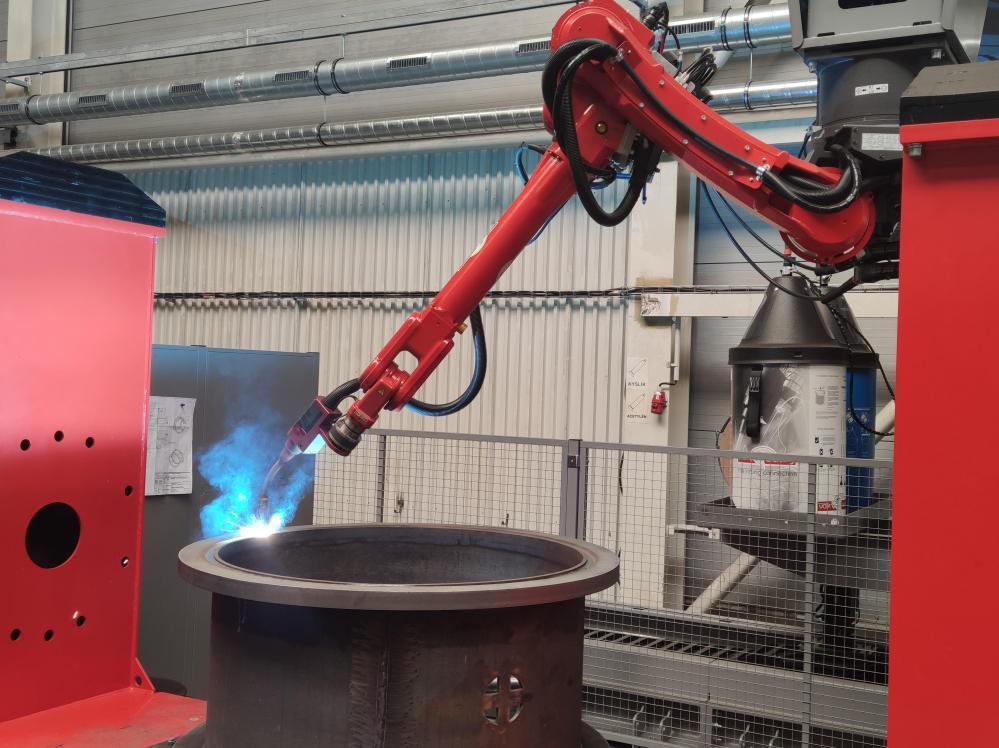
The supplier of the workplace is Valk Welding, which has many years of experience in the field of welding robots and many successful implementations. The installation of the equipment was completed at the end of June and the first welds are currently being programmed and welded with excellent results.
Operators were selected to operate and program this modern equipment and received specialized training divided into several specialized blocks. Programming of the equipment can be carried out directly on the part to be welded or off-line using software.
Workstation layout
The workstation is based on three welding stations and one suspended robotic arm. The Panasonic welding robotic arm, specially developed for arc welding in a protective gas atmosphere, moves along a linear line between the stations.
- the first station is equipped with a two-axis positioner with a load capacity of 2 000 kg and a space in the U-frame of the positioner of max. 2 600 mm
- the second station is equipped with a single-axis table with a load capacity of 3 000 kg
- the third station is a free area, designed for larger products
What the welding robot can do
The welding robot is equipped with a set of sensing elements and functions so that it can weld as many types of nowadays made welded joints as possible. The main types include multilayer fillet and butt weld joints.
The welding robot is equipped with automatic wire exchange, which allows the exchange of two different grades of welding wire without the need for operator intervention in the welding process. This application is applicable for example in shut-off valves, where in most cases two different welding wires are used.
To correct the inaccuracy of the position of individual parts, the device is equipped with a touch sensor. The touch sensor allows the position of the weldment to be sensed by the welding torch. After the position is sensed, the program is corrected according to the actual position.
The main expectations from modern welding equipment are:
- increased stability of the welding process
- significant reduction in working hours
- increase in quality of welded joints
- increase in welding capacity
- reduction of the number of mismatches
Types of products for welding robot
The concept of the welding robot workplace is universal and not limited to a specific product type from our product range. The only limitation is the load capacity and the size of the positioners. To reduce non-production times by programming, we focus on repeatability of weld types.
Currently, programs are created for welders with the highest repeatability. These include, for example, valve bodies for our sister company VEXVE.
This is a new stage of welding, and the ARMATURY Group believes that joint efforts will increase work efficiency, production capacity and the quality of welded valves.
For more information:
David Scheffczik, Head of TPV Welding