S33.4 gate valve optimization and order produced in record time
At the beginning of this year, the ARMATURY Group began discussing the idea of simplifying and speeding up the production of S33.4 welded gate valves while maintaining all measurable parameters (strength, tightness, deformation, etc.).
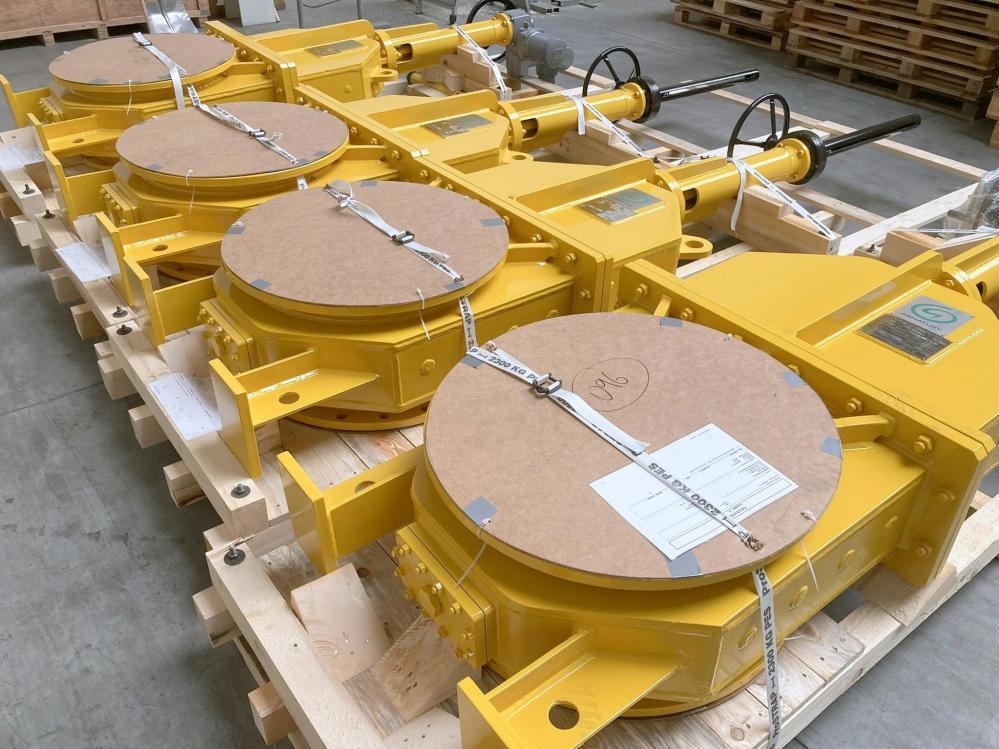
A contract for an end customer, Tata Steel, seemed the ideal opportunity to implement these ideas. One of the important points of this contract was also the short delivery time.
10 % lighter gate valves
To help with this task, the ARMATURY Group used a number of innovative tools such as topological optimization to generate a design based on boundary conditions. The result can be very interesting structures, as can be seen in the attached images.
As an inspiration for further work, topological optimization seems to be a very good tool. The next step in the endeavor is parametric optimization, in which we already compare the manufacturable part, where adjusting individual parameters such as the width and thickness of the sheets optimizes the final design. The result of this effort is a gate valve that has a weight reduction of 126 kg while maintaining the same stiffness, which corresponds to about 10 % of the gate valve weight.
All gate valves have passed pressure and function tests and have been delivered to the end customer. The disadvantage of the multiple topological and parametric optimization is the time-consuming nature of the whole process; on the other hand, the ARMATURY Group was able to remove some ribs and their welds in this piece in addition to reducing the weight.
Gate valves in record time
A contract for a long-standing customer, Tata Steel, was used to realise this idea. For this company, ARMATURY Group produced 4 pieces of welded gate valves S33.41 type 134 AG DN 600 within a very short deadline of 14 weeks from the order.
In July, pressure and functional tests were successfully carried out in the presence of the customer. In the first week of August, the gate valves were shipped to the port city of IJmuiden in the Netherlands, where they will replace the old pieces in the local steelworks and become part of a major investment in new technologies that will ensure the necessary reduction in CO2 emissions. The working medium will be coke oven gas.
Thanks to this success, the ARMATURY Group will soon be taking delivery of further S33.41 valves in larger sizes DN 1000 and DN 1800.
For more information:
Lukáš Kušnír, Director of Research and Development
Ján Puffler, Project Manager | Metallurgy
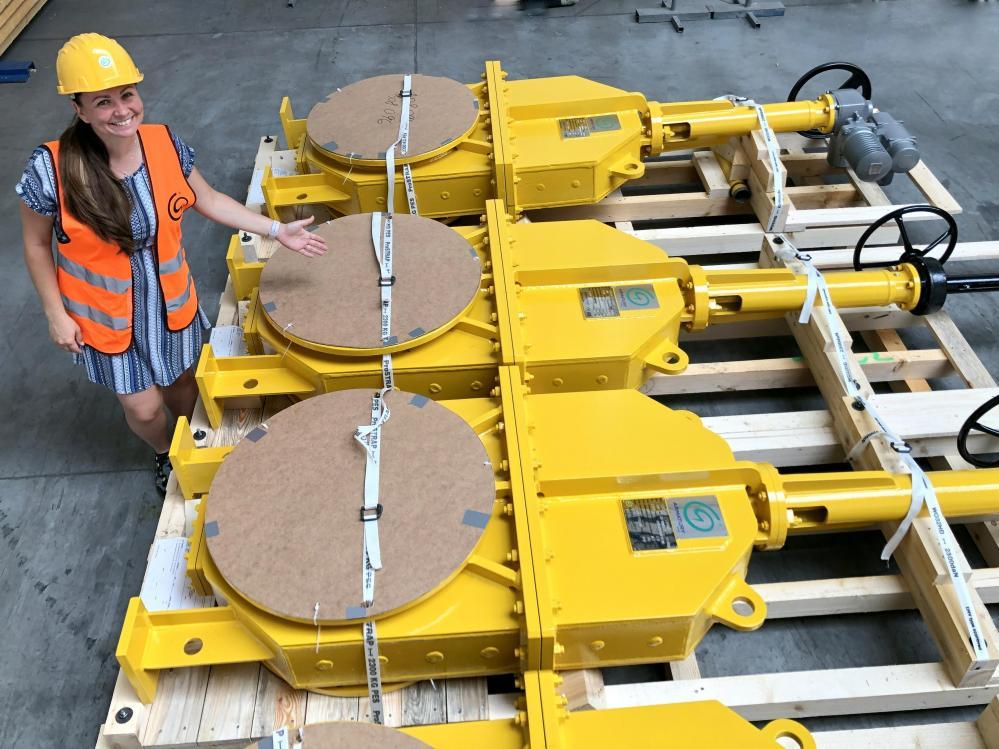
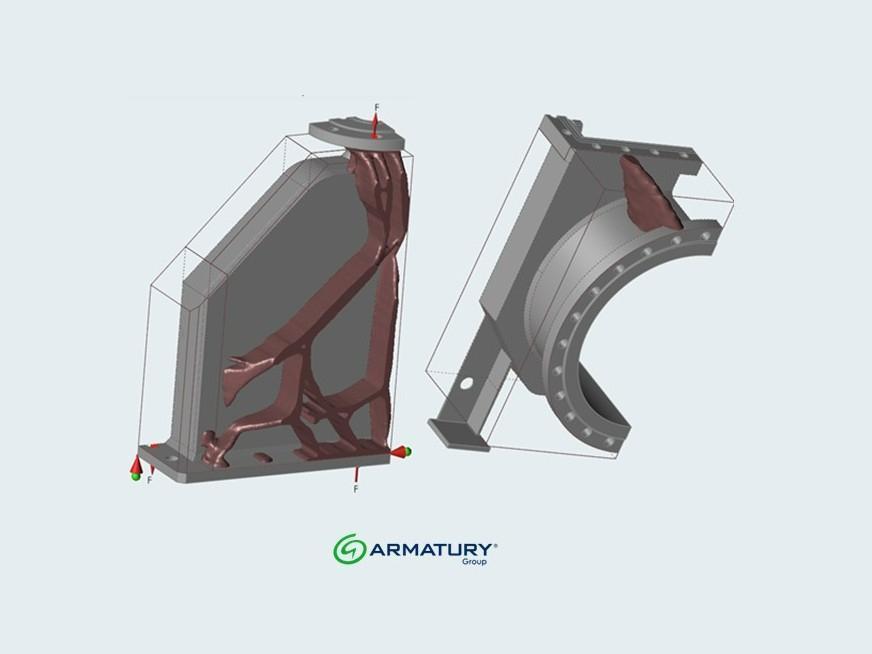
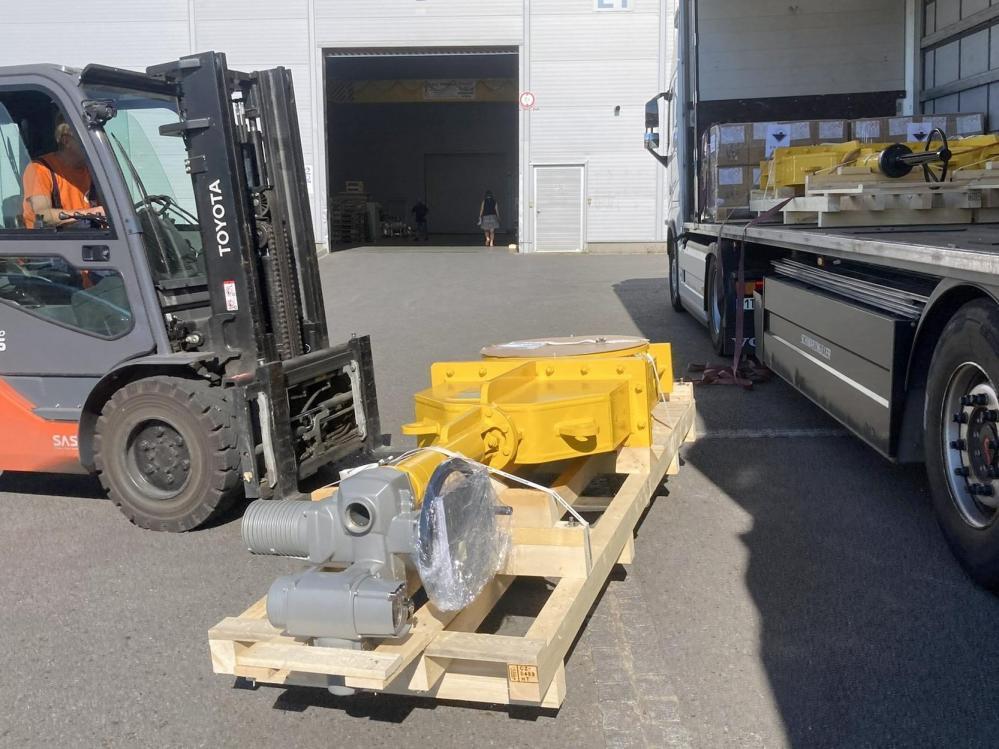