We work online – training, tests, inspections.
Although the number of infected is decreasing every day, we still must deal with security precautions.
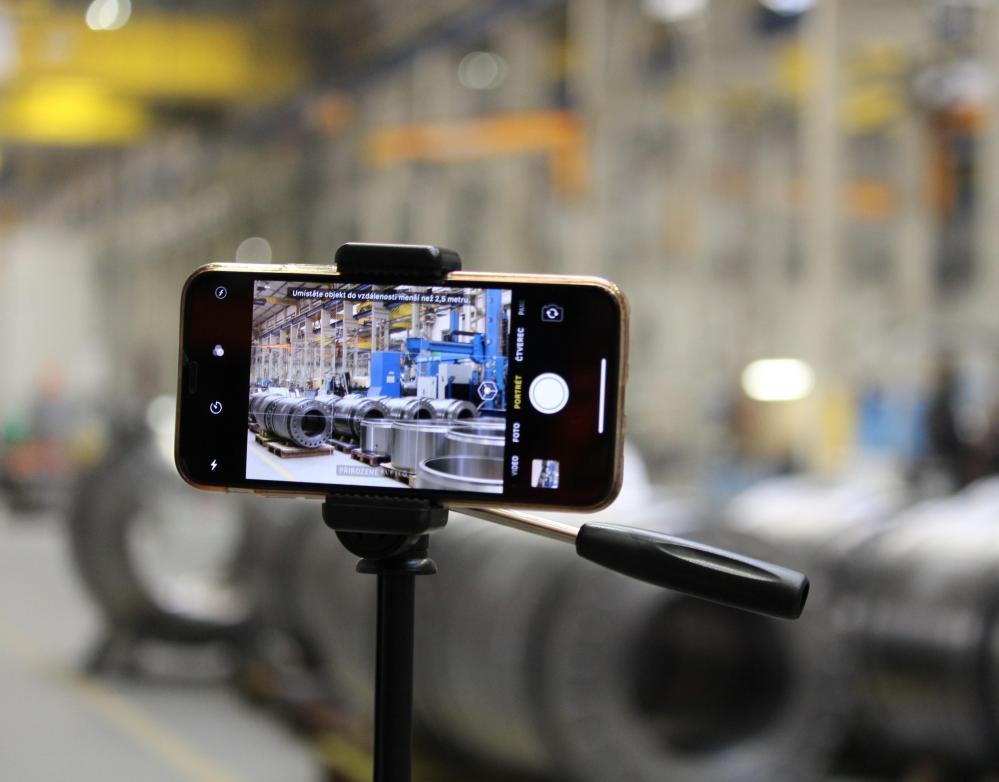
Online conferences, interviews, meetings and regular company meetings. But it does not end here. We had to adapt to this situation even in situations, where the preparation is longer than turning on the streaming application. We mean online training or inspections.
Training for Czech Gas Association
For many years we have been actively cooperating and attending meetings for the Czech Gas Association. We are also invited to solve problems at this level, we publish professional articles in the journal “Plyn” (Gas).
At the beginning of March, we were asked to help organize training about industrial valves in the gas industry for its members. The training was on 30 March and took a few days of preparation of presentations and training materials before.
First part of the training was about ball valves and other valves for the gas industry in the ARMATURY Group portfolio. In the second part, different types of controls that can be used on valves and their advantages were introduced to the participants.
The training was closed with information about the main activities of the “Service and repair of the valves” department, about valve repair and the most common mistakes during the assembly were also mentioned. Participant also learned, which repairs can be made at the customer and which one had to be done at our company.
We found a solution – online inspections!
More work required preparation for online inspections for the customers. It is not only about setting up a camera and pressing rec. button. It is necessary for such an inspection to find a good place, light and to have the necessary technique, tripod and in addition it is necessary to have an employee who will take care of the acceptance for the whole time!
Each inspection is different according to the customer. The inspection can be carried by the end customer or by a third party inspection.
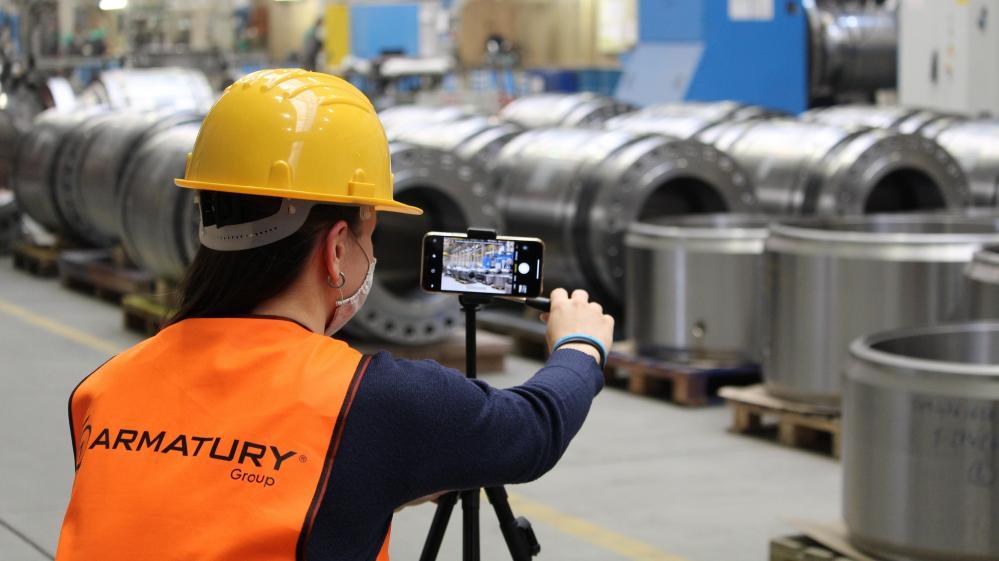

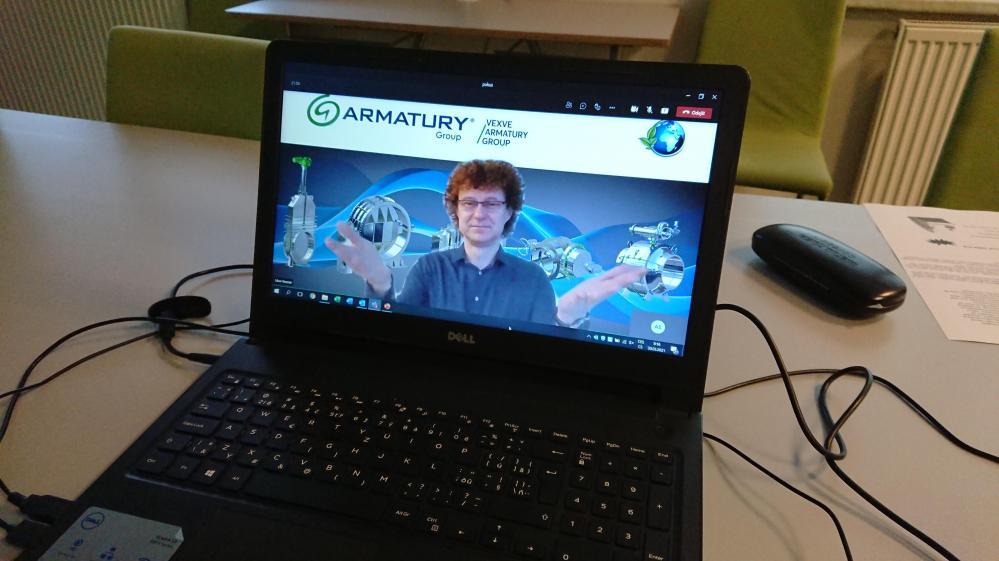

9 days online
There have been many online inspections during the pandemic. We can mention for example two inspections for the same customer. The first inspection took place last year. These were pressure tests when we were recording testing for a third party in Ukraine.
The third party wrote a final report for the end customer – Ukrtransnaft. The acceptance lasted a total of nine working days, in two-shift operation.
The second inspection for this customer was this year. It was a contract to produce 13 ball valves K92 (11 pieces DN 700 + 2 pieces DN 500). This acceptance also took a lot of time. While two-shift operation lasted 5 working days.
Online inspections took place via Microsoft Teams, while photos were sent to the customer via WhatsApp. The first acceptance was at the time, when a representative of our customer was present at ARMATURY Group and helped with the pressure test.
After that, however, there was a ban on visits at our company, so both our sales managers and quality controllers had to take turns at these inspections. It was very demanding for them, due to the working schedule.
Traditionally – Poland and Gaz-System
Due to the pandemic situation, many inspections were filmed also for our Polish customer Gaz-System. The acceptances were recorded for third party inspection, Bureau Veritas, and mainly concerned project Polska Litwa and Baltic-pipe.
Part of the inspection was pressure tests and test of surface treatment Protegol. For this customer we delivered many valves, for which have we to do several tests and issue many permits. We have been providing online inspections and examinations for more than a month until it was possible to arrange entry authorization of the representative.
This pandemic time is full of new expectation and obstacles. We at ARMATURY Group are happy that all these challenges move us forward in effort to continuously improve customer service.